Finite Element Analysis (FEA) To Save Costs in Product Development – How FEA Can Help Your Enterprise Stay Frugal
Finite element analysis (FEA) today is widely used for virtual prototyping, bringing about significant savings in terms of cost, time and resources. These savings are realized due to reduced number of physical prototypes and testing that is required to determine the possible outcomes. As a result, FEA is now widely used in many industries and below are a few examples of the various industries benefiting from FEA:
- Automotive – The most advanced applications and development of FEA occurs in the automotive industry. Here, FEA techniques are employed when designing automobile parts such as wheels, leaf springs, body and frame, shafts and in testing performance [1]. In addition, FEA simulations are used to model car crash analysis to identify critical factors paving the way for design improvements before performing NHTSA certification testing, thereby saving much time and money [2].
- Aerospace – FEA is heavily employed in the design of aerospace components, crash simulations [3], aircraft load calculations, analyzing landing gears as well as accidents like bird strikes and bird engine ingestion. With these simulations, the aerospace industry makes significant savings in terms of money [4], resources and time.
- Turbo Machinery – FEA effectually simulates complex geometrical shapes required for turbo blades with different attachments [5]. Various blade geometries and shapes can be analyzed rapidly and compared. With FEA, 5% of design and development cost savings were realized based on a case study [6].
- Industrial machinery and spare parts- A study was performed to measure the ROI of CAE for Domnick Hunter products such as Sanitary liquid housings and seals. Accordingly, it was shown that developing virtual prototypes could reduce 20% of the cost and 50% of time compared to conventional methods [7].
- Biomedical Applications: Soft tissue, bone, implants, medical devices, drug delivery systems, etc. are all modeled today with FEA simulation. Products made with complex biomaterials can now be evaluated with high fidelity using FEA.
- Construction: FEA is a highly effective tool for analyzing the physical structure when subjected to external loads such as gravity, wind, and natural disasters (earthquakes and tsunamis) and conditions such as sedimentation, erosion, and coastal flow problems. General analytical methods are complicated and often less accurate for complex building shapes or skyscrapers. FEA is an ideal tool to simulate the performance of innovative construction materials, complex geometries and loading conditions.
- In addition to the specific application areas mentioned above, scores of other product development industries such as electronics, packaging, heavy machinery, tools, sports technologies and even forensics have also incorporated FEA into different parts of their product life cycles. FEA benefits in greatly saving time, developing costs, reducing certification costs, improving accuracy and in facilitating innovation through varied analysis criteria.
- Massive Volume of Data:
The sheer volume of data that is generated through FEA analysis is almost impossible to get with physical tests. For example, it is often impossible to place gages at every location in a test article or even capture a video of certain areas of the test. An FEA analysis of such a test is capable of providing engineering data for all elements used to discretize the part. The 3D model can also be viewed from various angles along with section cuts for studying the test results. - Virtual Prototyping:
With FEA, it is possible to evaluate the design before creating the actual physical prototypes. How would material A fare in place of material B? Can the product design be optimized to reduce weight? Questions and concerns of this nature can easily be addressed promptly by utilizing the FEA instead of getting into a costly loop of preliminary product testing. The user, therefore, is presented with tremendous flexibility for swapping materials, altering the part geometry and loads working on the part. - Improved Quality with Minimal Waste in Product Development:
In a study by Aberdeen Strategy & Research the data showed that by using CAE tools in their workflows, companies were able to reduce prototypes by 27%, shorten the length of development time by 29%, reduce the number of engineering change orders by 21% and promote 2.5 times more collaboration amongst engineers [8]. The application of virtual product development tools such as FEA early in the design process is known as frontloading. There are clear benefits to this approach. It allows developers to get high quality data and insight on the product and mitigate failures later in the product life cycle [8].
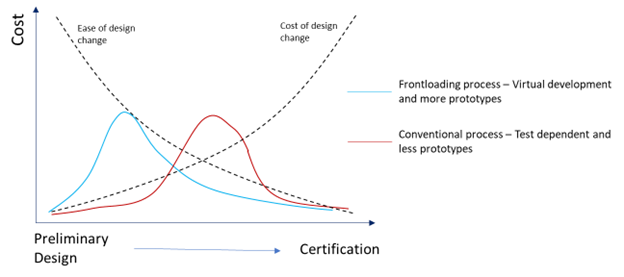
As much beneficial as FEA has proven to be, it does come with initial inescapable expenses which have to be considered carefully at the onset of a project.
These costs incurred are usually due to:
- Software: A typical FEA software license for a single user can vary between thousands to ten thousand dollars and may include maintenance costs. Also, if the user demands advanced functionalities or high processing power, the licensing may have to be upgraded accordingly.
- Ensuring hardware compatibility: Existing hardware should be compatible with the software requirements, and where it is not, an upgrade in hardware or purchasing of new hardware may be necessary to run the FEA simulators smoothly.
- Arguably, an FEA model is only as good as its analyst. The inherent potential of a good model therefore has to be tapped into frequently via training, knowledge transfer sessions and by incorporating it into the development process.
- Staff Recruiting and Retaining FEA knowledge: Recruiting an FEA expert or retaining an internally developed FEA expert can be challenging and expensive as such expertise is frequently sought after by design firms.
- Database Development: It may be vital to develop and maintain databases for FEA models, and additional hardware or cloud space may be needed for databases.
- However, the overall cost-effectiveness of employing FEA in enterprises is in effect relative to the number of projects that require FEA analysis. If, for instance, FEA is used continuously over long periods in different design projects within the same enterprise, not only does the cost of FEA analysis per project decrease, but the analysts too gain an edge over the specific domain, excelling at its design and execution during the period they are allocated to the project. This in turn serves to benefit the project as a whole ultimately with honed expertise, improved efficiency and sustainable growth.
References
[1] S. Gu, “Application of finite element method in mechanical design of automotive parts.,”
IOP Conference Series: Materials Science and Engineering,, vol. 231, no. 1, 2017.
[2] A. B. Pifko and R. Winter, “Theory and application of finite element analysis to structural crash simulation,” Computers and Structures, vol. 13, pp. 1-3, 1981.
[3] M. A. McCarthy, C. G. Harte, J. F. M. Wiggenraad, , A. Michielsen, D. Kohlgruber and A.Kamoulakos, “Finite element modelling of crash response of composite aerospace sub-floor structures,” Computational Mechanics, vol. 26, no. 3, 2000.
[4] Siemens, “Faster FEA improves productivity and saves tens of thousands of dollars,” Siemens, 2022. [Online]. Available: https://www.plm.automation.siemens.com/global/pl/our-story/customers/aquila-engineering/79642/. [Accessed 10 February 2022].
[5] M. H. Jalali, N. Nouri and S. Ziaei-Rad, “On The Finite Element Modeling Of Turbo Machinery Rotors In Rotor Dynamic Analysis,” in CSME Conference Proceedings, 2018.
[6] Genpact , “Design and development cost reduction through Finite Element analysis for a global power generation OE,” 2014. [Online]. Available: https://www.genpact.com/downloadable-content/insight/design-and-development-cost-reduction-through-finite-element-analysis-for-a-global-power-generation-oem.pdf. [Accessed 10 February 2022].
[7] D. Bosworth, “The Business Value of Simulation: Moving From FEA to ROI,” Autodesk, 2020 [Online]. Available: https://www.autodesk.com/autodesk-university/class/Business-Value- Simulation-Moving-FEA-ROI-2012. [Accessed 10 February 2022].
[8] Y. D’Arino, “HOW TO WRITE A BUSINESS CASE FOR CAE SOFTWARE,” 08 2021. [Online]. Available: https://www.dive-solutions.de/articles/business-case-for-cae-software. [Accessed 05 2022].
[9] Cyprien, “How to Reduce CAD Design Cost using simulation?,” FEA for All, 2014. [Online]. Available: https://feaforall.com/reduce-cad-design-cost-using-simulation/. [Accessed 10 February 2022].